Plans
You can download the CAD drawings of my devices in order to produce your own, but everyone’s tools and materials vary. Instead of constraining you into my designs, I will put emphasis on tips and tricks on how to design your own with your available resources.
Particular Parts
Here is a list of particular pieces used in this project. There are some notes for each of them, documenting what I found to be good characteristics to build a satisfying device.
-laser
Any visible dot laser should do. A basic red laser pointer will do the trick, but lacks
brightness. A 5mw green laser module works great. Even better if they react well to pulsing
(~500 hertz). There are plenty of suppliers on-line, eBay, deal extreme and other laser
specific re-sellers. Getting a pair of safety eye wear corresponding to your laser’s wavelength is recommended.
-speakers
The main attraction of the speaker is its linear movement. Sub woofers are ideal, due do the distance traveled
by the cone. But sub woofers are large and loud. A smaller (~30mm) “full range” speaker tend to work well.
A durable cone helps connecting the speaker to the mirror.
-amplifier
Since these devices act closely to oscilloscopes, the amplifier plays a big role in the produced shape.
Different amplifier classes will amplify the sound in different ways, producing different shapes. Class
A or AB seem to work well.
-mirrors
Pretty much any small mirror will work. Ideally: front silvered, thick, narrow (~10mm). This can be
scavenged out of laser printers.
-screws
Threaded pointy ones. Smaller threads are nice.
The Mechanism
The goal is to convert the speakers linear motion to rotary motion. There is not much more to this device than two of these, perpendicular and upside down from each other.
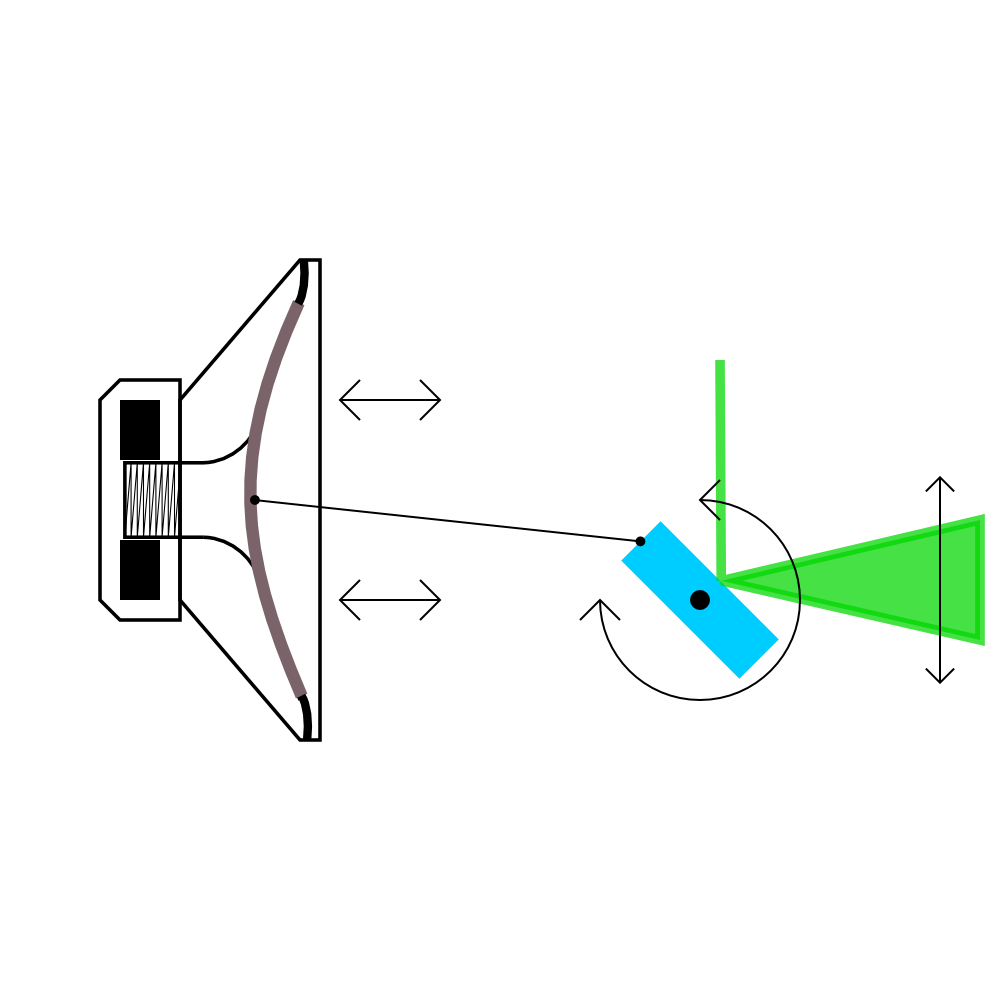
Building the Mechanism
There are some particular methods to building this mechanism.
-mirror pivots
The mirrors, roughly ~8mm X ~10mm, are drilled on two opposite ends. The pointy screws will rest at the bottom
of these shallow holes. A long front silvered mirror from a laser printer is ideal, it can be cut into smaller
pieces with a rotating tool cutting disc. Drilling the mirrors is very tricky. Scoring an cross on the mirror
with the cutting disc can help start the drilling process on the center point. Drill very slowly using a drill
bit of roughly ~1.5mm diameter. The hole does not need to be deep, it simply has to provide a “>” for the
point of the pointy screw. The screws should go into plastic material, thick enough for the screw to be able
to be adjusted back in forth. The material should also provide flex in order to apply the right amount of
pressure to the mirror. Just tight enough so it dose not rattle and loose enough to let it rotate freely.
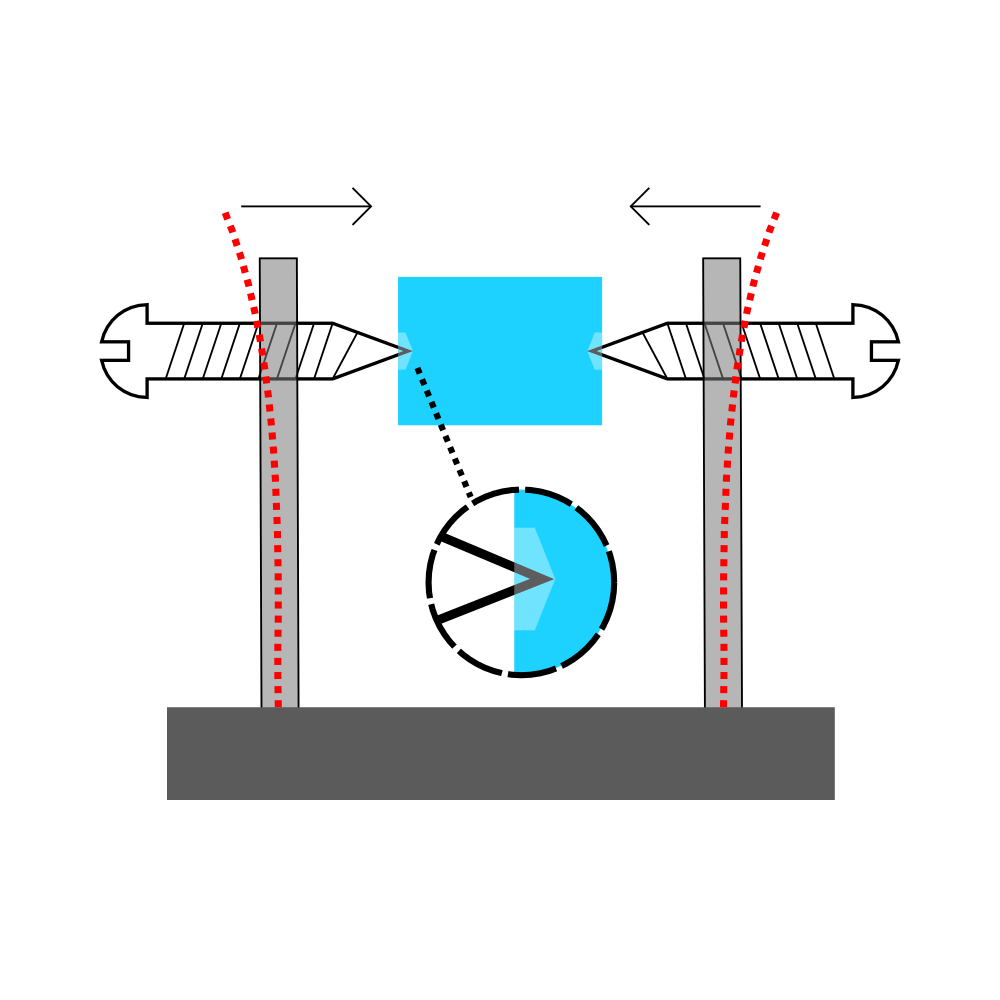
-linkage system
The linkage system is made of solid core wire and hot glue. Bending a “Z” in the wire provides an adjustment
method. Bending the middle section will allow to tune the mechanism, sending the laser beam straight from
one mirror to an other and straight out. One end is hot glued to the speaker, the other to the mirror. On the
mirror side, a certain amount of swivel is needed at the joint. This is achieved by very slightly lubricating
the end of the wire. Once the glue cools, the wire should be able to swivel inside the glue, without allowing
much play.
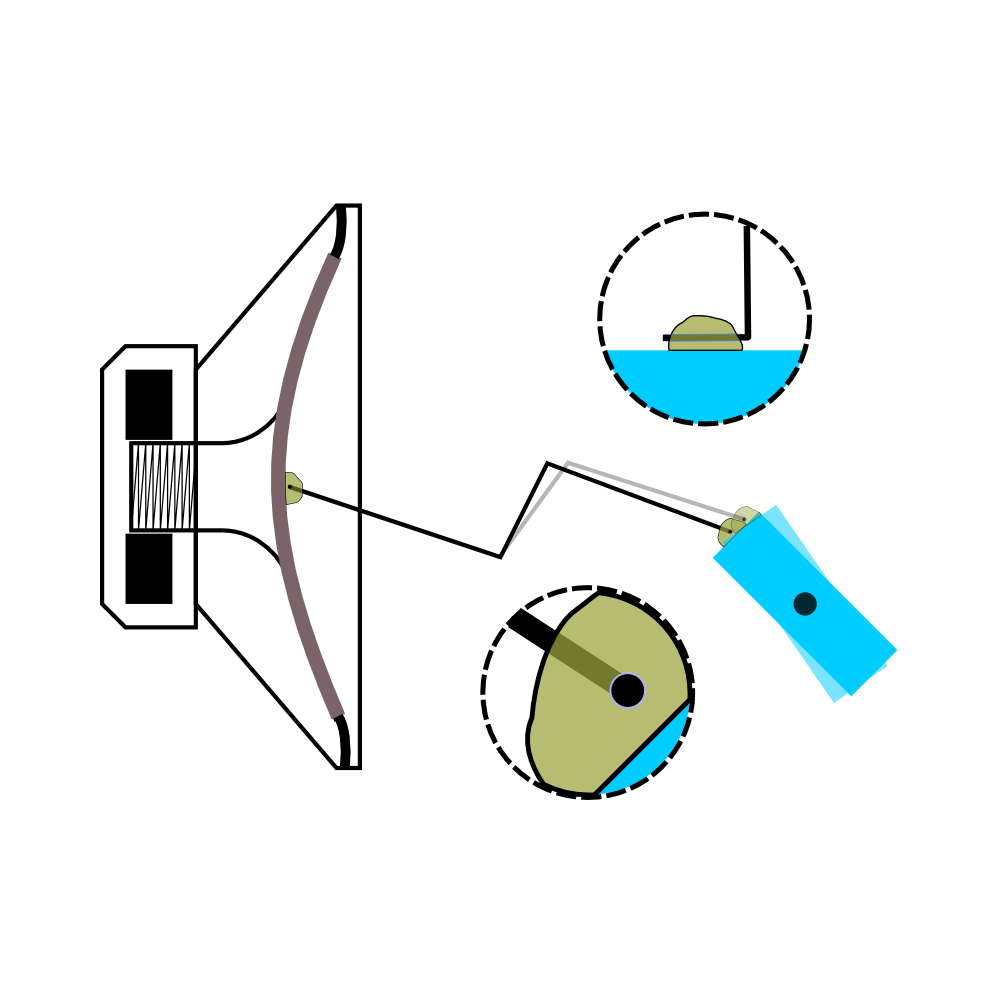
Assembly
Basically two of these mechanisms need to be assembled together with the laser. The two speaker and mirror assemblies should be positioned perpendicular from on and another. This way the beam hits the first mirror, modulating horizontally, and hits the second mirror, modulating vertically. Keep in mind to have access to the pointy screws to adjust your mirrors. Here is the top view and side view of the essential elements.
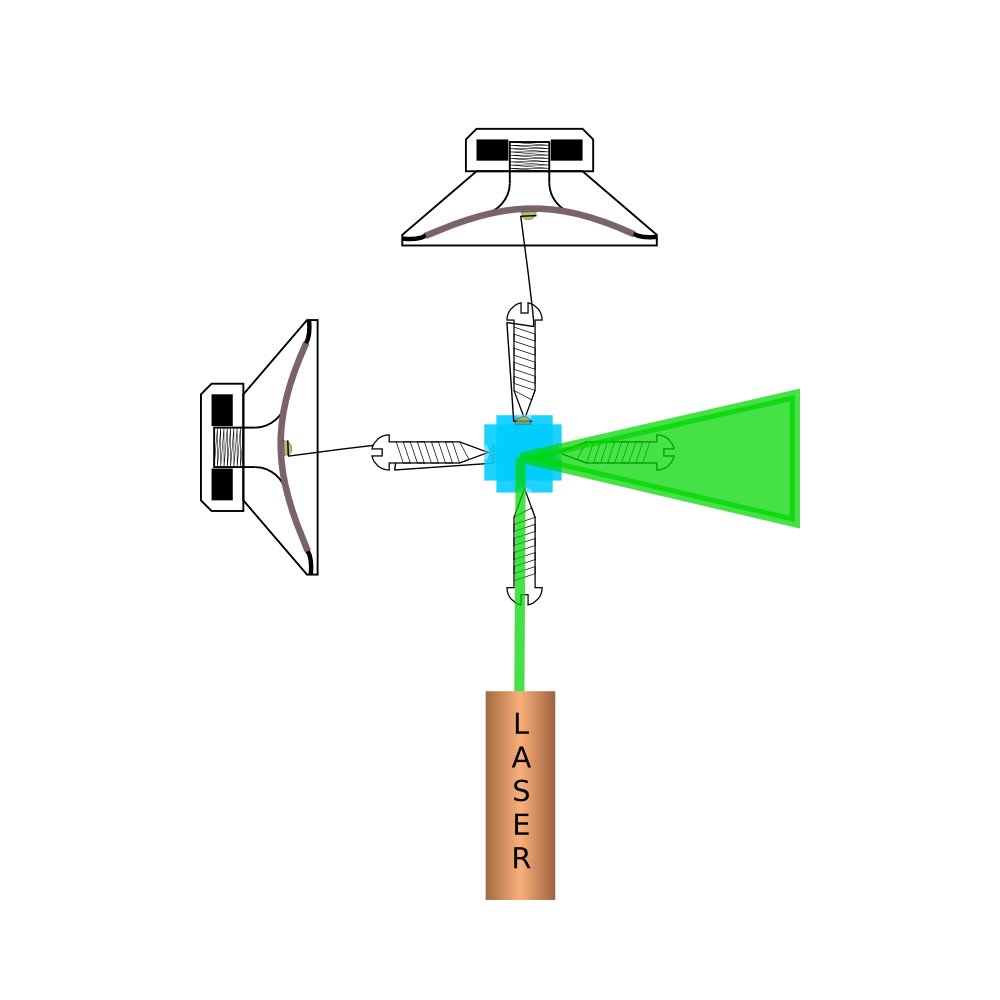
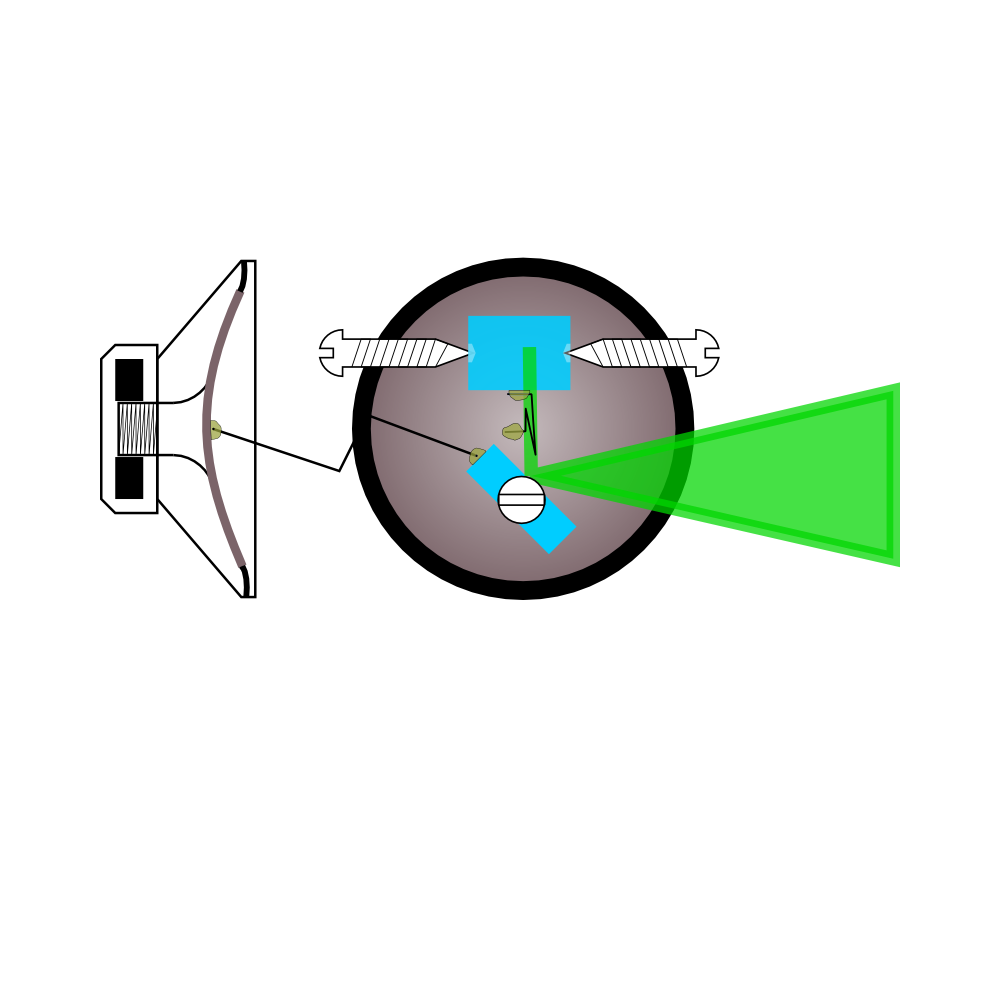